A quick search for ‘UAE construction projects’ will reveal the immense scale and ambition behind some of the world’s most cutting-edge developments.
These projects, many of which are shaping the skyline of cities like Dubai and Abu Dhabi, demand more than just conventional building methods. To meet the tight schedules and high-quality demands, one of the most effective approaches being employed is modular construction.
What is modular construction?
Modular construction involves the off-site production of smaller or unified components of a structure, which are later assembled on-site. This method is quickly gaining traction across sectors, from energy and health to transport and tourism, for one simple reason: speed. According to McKinsey & Company, prefabricating key components while site preparation is underway can shorten the overall construction timeline by up to 50%*.
This is critical for the UAE, where rapid execution is often a priority. Construction Week Middle East recently highlighted this trend, noting that the modular construction industry in the GCC grew from $2.9 billion in 2020 to $3.4 billion by 2023. As projects become more complex and time-sensitive, the shift toward modularisation is becoming increasingly necessary for delivering results that are faster, more efficient, and more sustainable.
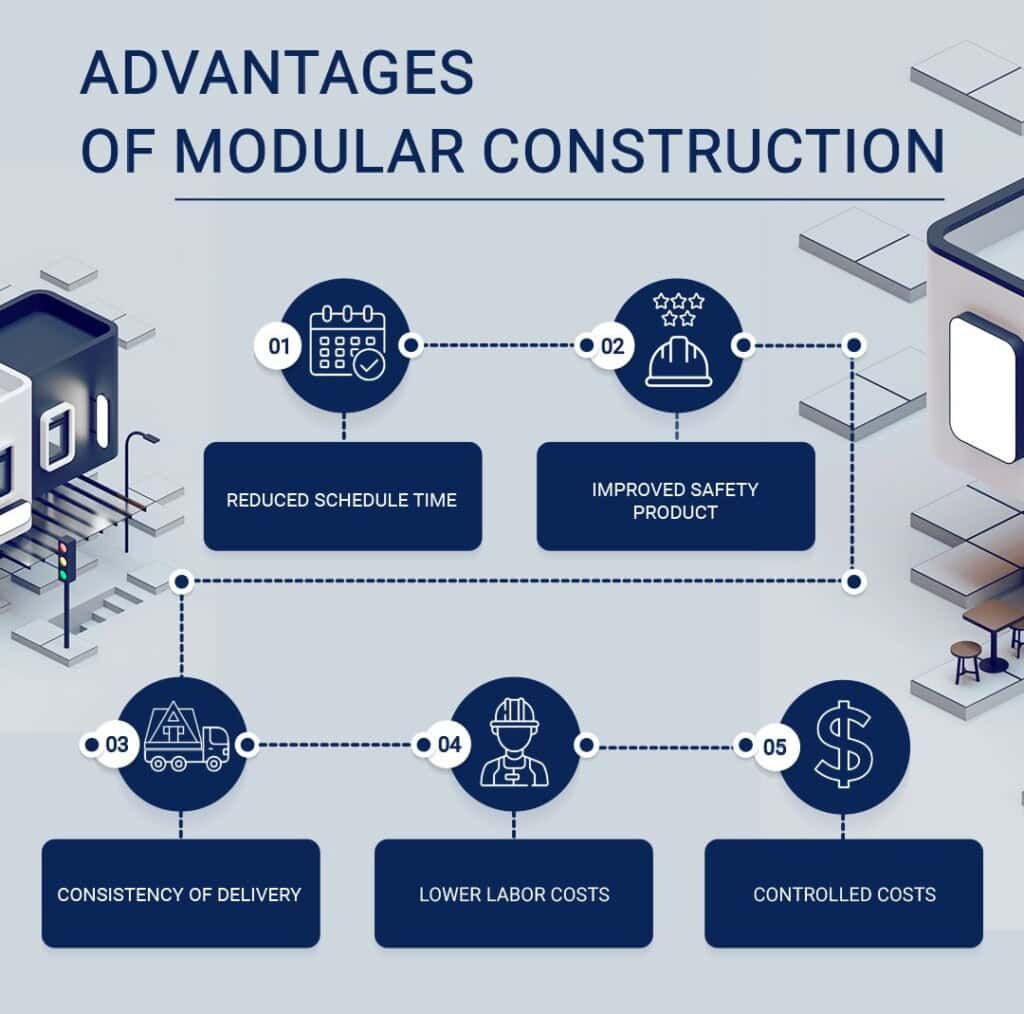
Efficiency meets sustainability
Modular construction is increasingly recognised for its ability to enhance project management and streamline the delivery of large-scale infrastructure projects. By allowing components to be prefabricated off-site, this method reduces not only time and resource requirements but also on-site disruptions, leading to a more efficient process overall.
In addition to these operational benefits, modular construction offers significant environmental advantages. By minimising waste, reducing transportation needs, and lowering energy consumption, this approach aligns well with global sustainability goals. As the UAE continues its efforts toward a greener and more sustainable future, modular construction will play a pivotal role in reducing the environmental impact of large-scale developments.
Key benefits for Project Managers
For Project Managers (PMs), integrating modular construction into their strategies is no longer just an option – it’s becoming a necessity. As we see the shift towards modularisation gaining momentum, PMs must be proactive in adopting this approach to ensure they remain competitive and capable of leading successful projects.
By adopting modular construction, PMs can leverage several key benefits, including:
- Faster build times – Components are built off-site while on-site work progresses, accelerating project timelines.
- Improved quality control – Factory production environments allow for tighter quality assurance compared to traditional on-site construction.
- Cost savings – Reduced labour costs and more controlled spending make modular construction a financially attractive option.
- Reduced waste – Prefabrication significantly minimises material waste, supporting sustainability initiatives.
As highlighted in the accompanying image, modular construction offers a range of additional advantages, including enhanced safety, consistency in delivery, and controlled project costs. These advantages not only improve project outcomes but also position PMs to handle the increasingly complex demands of modern construction in the UAE.
Leading the future of construction
At Rider Levett Bucknall, we are dedicated to staying at the forefront of this growing trend. Modular construction is set to redefine how we approach project planning and execution across the UAE and beyond. By embracing modularisation, project managers will be equipped to meet the challenges of today’s ambitious projects, delivering results that are faster, more cost-effective, and more sustainable.
FURTHER INFORMATION:
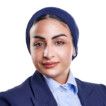