DAIM Building
In early 2022, The University of Hull sought to deliver a step-change in the provision of its teaching excellence, quality research, and knowledge exchange for its Centre of Excellence for Data Science, Artificial Intelligence and Modelling (DAIM). Through assured project management and the innovative use of modern construction methods, less than 12 months later, the university opened its new £4.5 million flagship for computational teaching and research.
Equipped with state-of-the art laboratories and hi-tech equipment, the transformational DAIM Centre delivers much-needed additional capacity for students and researchers to learn, practice, and apply computer and data science knowledge and skills. Delivered on time, in budget and with minimal disruption, the new facility will enable Hull to fulfil growing application numbers for computer science studies and further its research ambitions.
At a glance
- ClientUniversity of Hull
- ServicesCommercial Success, Built Asset Consultancy, Project & Programme Success, Project Delivery, Project Management, Cost Benchmarking and Cost Intelligence, CDM and Principal Designer
- sectorEducation & Research
- LocationHull, United Kingdom
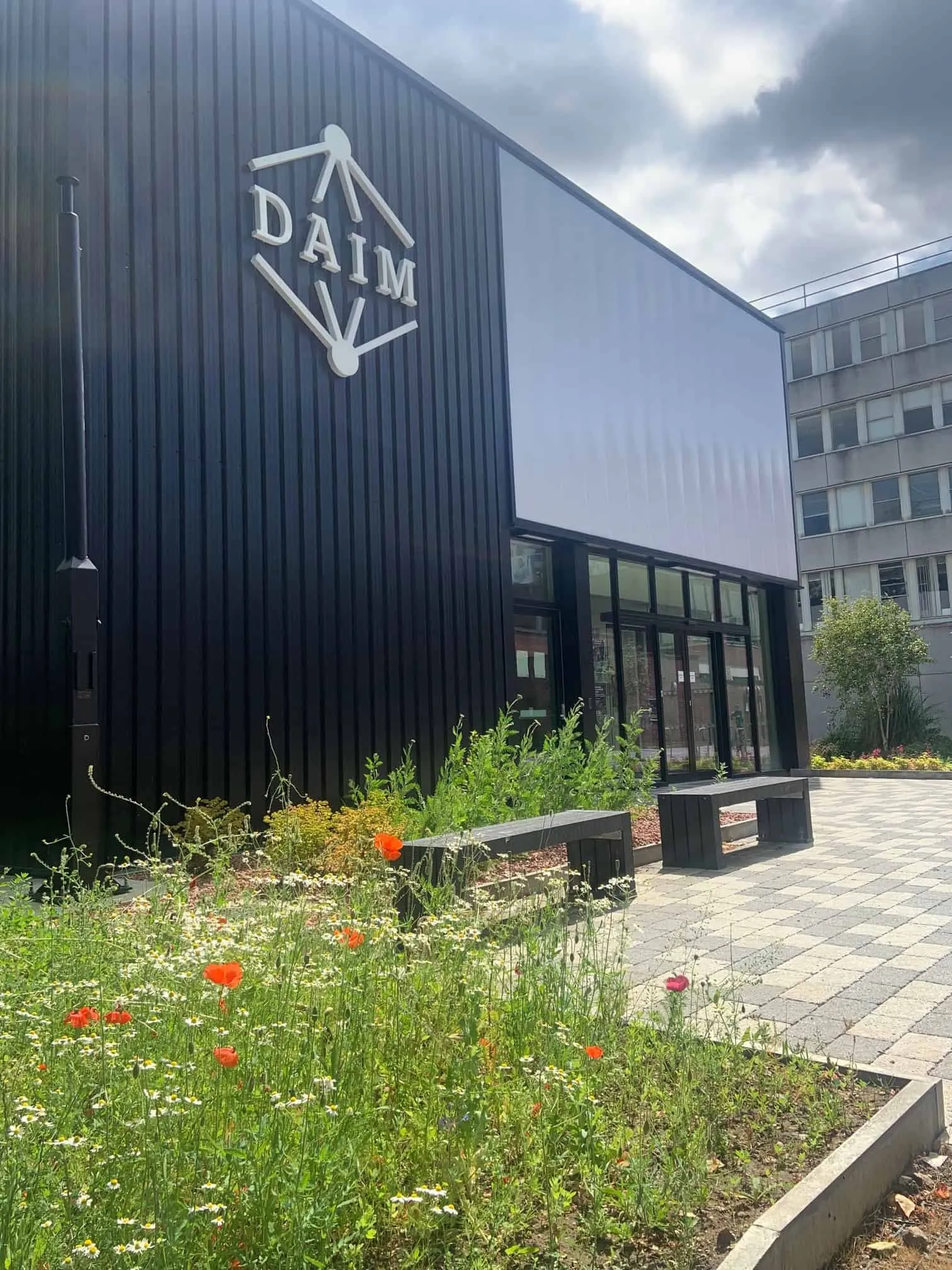
Navigating a challenging timetable
At the forefront of exciting developments in AI and data science fields, the University of Hull had ambitions for a building that would deliver cutting-edge equipment with manageable running costs, but would also support its target to be carbon neutral by 2027 – its centenary year. Crucially, it needed a solution in place within a six-month timescale, ready to accommodate a new cohort of international students eager to start their studies. RLB approached the project with the ethos of providing a smarter, greener and better solution, from initial construction to ongoing use. Following a feasibility study that revealed that existing available space was not conducive to open plan IT Lab requirement, and traditional construction methods for a new build would exceed time constraints, attention turned to an innovative new-build approach.
The team concluded that a modular construction method would reduce construction time by approximately 10 – 12 weeks over traditional new-build. By negotiating contracts with a local modular supplier and sub-contractor, waste and carbon could also be reduced by using refurbished modular units. The construction method would also minimise material deliveries to site and limit noise and vibration disruption to surrounding academic buildings in a live campus environment. Using off-site construction in a factory environment also eliminated site-based construction risks and processes, and removed the risk of delay due to material shortages and weather conditions.
"The building is testament to an outstanding collaborative approach by the full project team. Through excellent consultant project management, local supply chains, passionate end-users, Estates, ICT and senior management, a significant opportunity was successfully met within a short period of time. The project is an excellent example of what can be achieved with innovative construction and delivery methods.”Stephen Dale, Director of Estates and Facilities
Integrating innovation with collaboration
Once the approach was approved, the team brought the delivery partners on board, using a cohesive team and a local supplier network. The client, including the Estates Department, ICT Department and Faculty, the design team and delivery team, all worked in a spirit of cooperation to ensure the building would open on time, holding weekly meetings to ensure smooth delivery. Ready for the start of the new academic term in January 2023, the building was delivered with minimal disruption to staff and students.
Integrating a local supply chain and using refurbished modular units is only part of the sustainability success story. RLB’s architectural and M&E designers embedded further benefits into the design that will provide long-term ESG rewards. These features include high insulation to reduce energy consumption, energy efficient LED lighting and lighting controls to all areas, a 28kw solar photo voltaic array positioned on the roof to self-generate electricity, and an energy efficient heat recovery system to heat and cool the building. The result is an A-rated energy rating under the Energy Performance Certificate assessment.
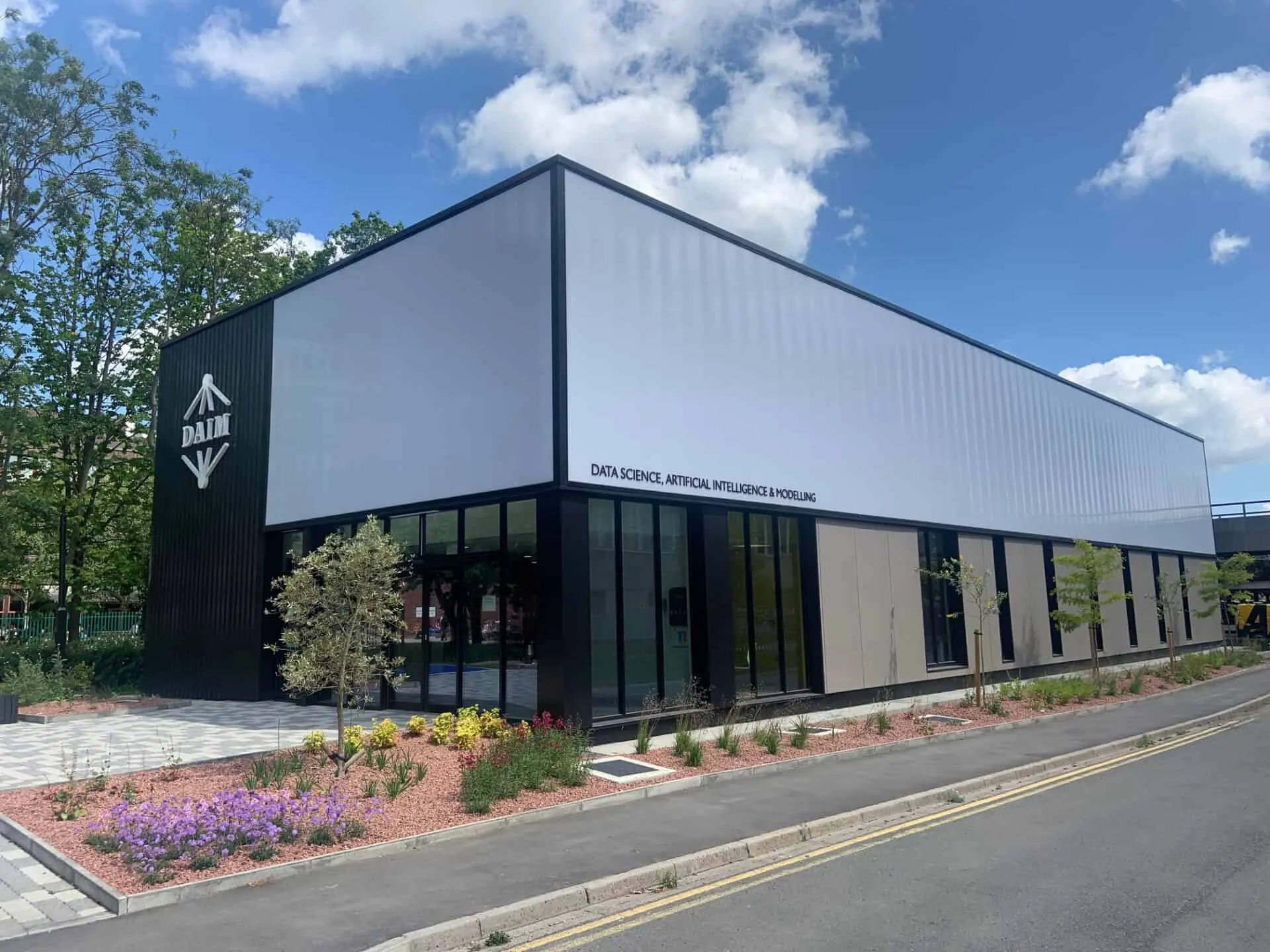
FURTHER INFORMATION:
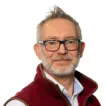
Paul Batchelor
Services
Sector
Related and Notable Projects...
-
Transforming a heritage brewery into an ecosystem for construction excellence
SCHOOL OF ARCHITECTURE AND BUILT ENVIRONMENT
View -
Estate rationalisation, creating a state-of-the-art research and teaching facility
UNIVERSITY OF READING HEALTH & LIFE SCIENCES
View -
Complex multi-phase refurbishment to create inspiring art & media facilities
KINGSTON SCHOOL OF ART, KNIGHTS PARK
View