Talk of a united, collaborative construction industry is fine, but how do we get the message out to all those working in it? There may be a price to pay to achieve the goal of whole-sector improvement.
It is a myth that there is no innovation or development in the construction industry. But it is true that improvement in construction productivity in the last 10 years has fallen well short of other industries. At the same time, we know that productivity on the best construction projects is 30% higher than the average – so why aren’t we all madly copying each other and implementing best practice?
In my roles both as global board director at Rider Levett Bucknall and as a member of the Construction Leadership Council (CLC) this is a question I have been asked, and asked myself, a lot recently. How do we get what we learn about best practice across to those who are actually “doing stuff”? As Andy Mitchell, the newly appointed chair of the CLC, moves it into the implementation phase of the Industrial Strategy construction sector deal, one of our key objectives is to engage as widely as possible, and ensure that we are not just talking to the same group of people all the time.
Part of the issue is structural. At the last count we had roughly 2.4 million people working in the construction industry. About 300,000 are members of professional institutions and another 600,000 or so work for companies that are members of trade bodies. The remaining 1.5 million are mainly self-employed or work for micro-businesses. That’s over 60% of the workforce not associated with any professional institution or trade body. Trade union membership within the construction industry is also at an all-time low. Even the CITB, the most wide-reaching industry body, doesn’t cover all areas of the workforce. There is no way to deliver best practice to everyone.
What can we learn from other industries and how they assimilate best practice, innovation and knowledge into everyday delivery? For example, in the healthcare industry, Nice (the National Institute for Health and Care Excellence) has made significant inroads in reducing the variation in the availability and quality of NHS treatments and care. Nice is operationally independent of the government, and its guidance and recommendations are made by independent committees. Or education – where Ofsted’s goal is to achieve excellence in education and skills for learners of all ages, reporting directly to parliament but with a mandate of independence and impartiality. What is the construction industry equivalent? Is there one? Should there be one?
In terms of annual expenditure, construction’s £110bn sits between health’s £190bn and education’s £100bn. The primary difference is that health is around 80% publicly funded, education around 90%, and construction only around 30%. Improving the industry is very unlikely to be led by the government – other than in very particular circumstances such as the Hackitt review. We will need to push this forward ourselves.
The government’s construction sector deal reaffirms the ambitious targets of the 2025 Construction Strategy – to substantially reduce carbon, time and cost in the sector and increase exports. We have an ample body of knowledge that demonstrates where and how these targets are already being met. The overwhelming challenges for the industry now are those of dissemination, then uptake, consistency, standardisation and quality control.
I do feel that change is in the air. The work done by the joint industry response group, made up of the principal representative groups from construction, in the wake of Grenfell has been widely acclaimed as a very good example of industry cohesion; there are strong and growing social media network groups for sole traders to share and offer advice and support to each other. Also, many of the larger firms are using up surplus apprenticeship levy funds to cascade training and development through their supply chains.
We have the Transforming Construction Alliance – which has considerable government funding to deliver an ambitious programme of industry-wide change through the Core Innovation Hub. We have a new body – Network Plus – funded as part of the construction sector deal, to drive a co-ordinated and effective approach to research resources. We have i3P – the infrastructure industry-funded innovation and development platform, and Constructing Excellence, and the Designing Buildings Wiki – the most widely used online information tool within our sector.
But there is still rivalry between construction disciplines, commercial pressure leading to lack of co-operation even within supply chains and a fierce protection of ideas (even bad ones). If we genuinely want to work in a collaborative industry then we all need to accept that we will have to collaborate at the highest level – across academic and professional institutions, trade bodies, advisory groups and large companies.
We need to really think before we create yet another specialist group, research project or website – and ask whether our time would be better spent contributing to and improving something that already exists.
And – at the very heart of collaboration – we may have to give up some personal “sacred cows”– or at least re-direct existing resources – for the greater good.
Ann Bentley is a global board director of Rider Levett Bucknall, a member of the UK government’s Construction Leadership Council and also a member of the CBI’s Construction Council
FURTHER INFORMATION:
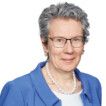