Quality is a word that is frequently bandied around in construction, yet for all the rhetoric, it still remains a significant challenge for our sector.
In its report Strategy for Change, the GIRI (Get It Right Initiative) estimated that the built environment is losing £10-£ 25billion in unmeasured direct costs of avoidable errors per annum, equating to up to 25% of project value.
World Quality Week, which took place last week, was a reminder that now is the time to understand why as an industry we need to focus on quality, learn lessons from the past and move from the rhetoric of quality to the reality of it on our construction sites.
Why does the built environment still struggle with quality?
Progress has been steadily made in the industry when it comes to collaboration, continuous improvement, sustainability, and innovation in construction projects with numerous guidance and governance coming into play including the Latham Report in 1994, the Egan Report in 1998, the Wolstenholme report in 2009 and the recent Building Safety Act. However tight margins, pressures on main contractors, legacy issues post completion and time pressures for delivery all continue to affect the quality of our projects.
Benefits of getting it right
Where cost still remains king when it comes to outcomes, high-quality construction minimises errors and defects, reducing the need for costly rework and repairs. Less rework in turn leads to projects on schedule and the reduction of additional resources, keeping cost and timeline intact.
However, cost isn’t the only consideration when it comes to quality – delivering high-quality projects builds client trust, leading to repeat business and positive referrals as well as the boost of morale and productivity for those working on a high-quality project.
Increasing quality, reducing environmental impact
With the drive for net zero across the industry, and pressures from investors on the ESG credentials of all projects, increasing quality will reduce the project’s environment footprint through efficient use of materials and energy. Getting it right first time will reduce waste, minimise reworks and contribute to environment conservation.
So how do we ensure quality is at the core of all we do?
Firstly, we need to look at a pre-emptive approach to managing quality risk and deliverables. Early engagement, bringing the right team together to plan and agree quality deliverables for the work is essential. This includes engaging designer, manufacturer, contractor, and subcontractor from the get-go. Quality professionals who understand the process and technical aspects need to embed a collaborative approach early in the process so that all stakeholders understand the part they own in the process to ensure quality.
The quality management team needs to be wider than the clerk of works with a focus throughout the whole project, bespoke to the project’s risks. A clear quality plan from the outset should be drafted, agreed and written into the project and contract documents. This will include setting clear client quality objectives, agreeing on roles and responsibilities concerning quality, and developing quality procedures that can be easily adopted and implemented across teams. There might be a further need for coaching or mentoring and supporting the contractor in the delivery of this quality too.
The role of digitalisation
With our industry already on its digital transformation journey, the adoption of digital tools is key to underpin delivery of quality. Although, as the GIRI highlights, digital implementation can be more challenging at site level due to employee resistance and lack of digital skills[1], gathering useable, real-time data throughout the project and having consultants onboard who can understand and analyse these insights can improve visibility while ensuring that there is one version of the truth.
Setting up digital dashboards that are woven into tender and contracts can support quality throughout the project but also provide the golden thread of information, as well as adhering to the Construction Leadership Council (CLC) guidance, that allows those involved in the maintenance and longevity of the project to understand what, how and why of the design and build, hopefully futureproofing the quality aspect for years to come.
We also know comprehensive use of digital tools to inspect and review the work progressively as it is undertaken and identifying earlier any rework that needs to be undertaken gives more time to the teams to address issues, minimising the impact on schedule and cost as well as reducing the health and safety risks. In turn this resulting in a higher chance of contractual handovers or practical completion defect-free.
Quality should be a given
Quality should be a given, not a variable, in the built environment. It makes not just financial sense but also makes real sustainable sense for our estates. However, we need to rethink our approach to quality, change the mindset of quality as a tick-box exercise and remember what Peter Drucker famously stated, “what gets measured, gets managed.” Using the right tools, engaging the right teams early in the process and progressively inspecting quality from the outset, will result in a pre-emptive risk-based approach, saving time, money and resources.
FURTHER INFORMATION:
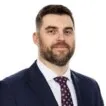